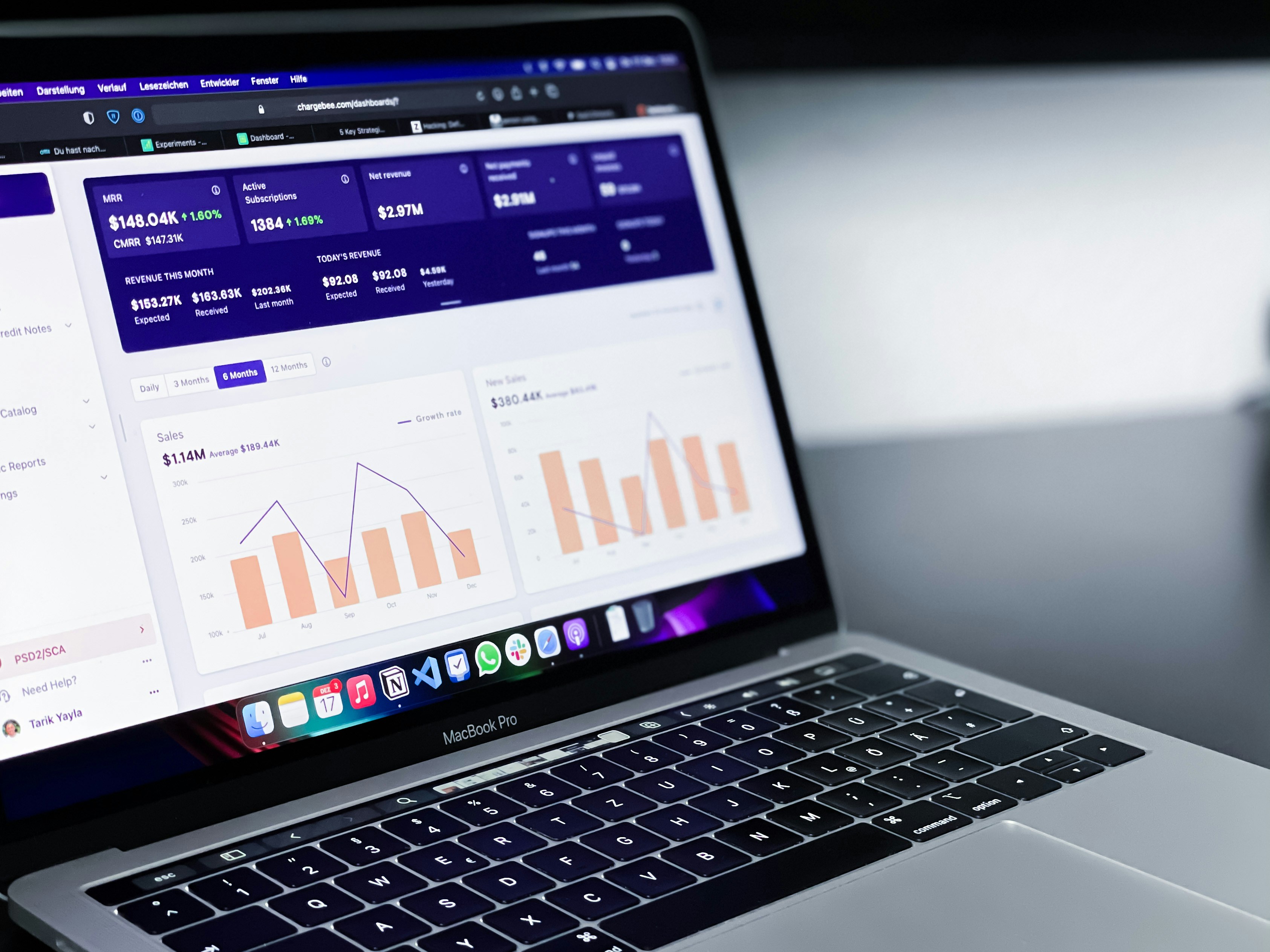
Introduction
Background of the Company
Kansai Nerolac Paints Ltd. (KNPL) is a prominent player in the paints and coatings industry, primarily operating in India and several other countries. As a subsidiary of Kansai Paints Co., Ltd., KNPL specializes in various products, including decorative paints, automotive coatings, and industrial coatings. With a robust network of over 29,500 dealers and multiple manufacturing plants across India, KNPL has established itself as a market leader in the automotive coatings sector.
The company faced significant challenges in managing production schedules across its multiple product lines, which led to inefficiencies and increased lead times.
Purpose of the Case Study
The primary objective of this case study is to explore how KNPL sought to address its production planning challenges by implementing an advanced solution. The goal was to enhance operational efficiency and streamline production scheduling through automation.
The Challenge
Detailed Description of the Problem
KNPL encountered specific issues related to production planning, including:
- Inefficient scheduling processes that resulted in delays.
- Difficulty in managing inventory levels across various product lines.
- Increased lead times that affected customer satisfaction.
These challenges not only impacted operational efficiency but also threatened KNPL's competitive edge in the market.
Why the Company Needed a Solution
The urgency for a solution stemmed from:
- The potential loss of market share due to delays in product delivery.
- Increased operational costs associated with inefficient production planning.
- The necessity to maintain high customer satisfaction levels amidst growing competition.
The Solution
Description of the Solution
To tackle these challenges, KNPL implemented SAP Material Requirements Planning (MRP) software. This solution automated and optimized the production scheduling process, allowing for real-time adjustments based on demand and inventory levels.
Key Features and Benefits
- Automation: Reduced manual intervention in scheduling, leading to fewer errors.
- Real-Time Data: Provided insights into inventory levels and production needs.
- Improved Scheduling: Enhanced organization of production schedules, minimizing downtime and bottlenecks.
Implementation Process
Steps Taken
- Planning and Preparation: Conducted thorough assessments of existing processes and identified areas for improvement.
- Execution and Deployment: Rolled out the SAP MRP system across all relevant departments.
- Training and Support: Provided comprehensive training for staff to ensure effective use of the new system.
Challenges Faced During Implementation
During implementation, KNPL faced resistance from employees accustomed to traditional methods. To overcome this, management emphasized the benefits of the new system through workshops and continuous support.
Results and Outcomes
Quantitative Results
- Increased production efficiency by 25%.
- Reduced lead time by 15%, significantly improving delivery schedules.
Qualitative Results
Stakeholders reported improved morale among employees due to streamlined processes. Customer feedback indicated higher satisfaction levels due to timely deliveries.
Conclusion
Summary of the Case Study
This case study highlights how Kansai Nerolac Paints successfully addressed its production planning challenges by implementing SAP MRP. The solution not only improved efficiency but also enhanced customer satisfaction through reduced lead times.
Lessons Learned
Key insights from this project include:
- The importance of employee buy-in for successful implementation.
- Continuous monitoring and adjustments are crucial for optimizing new systems.
- Investing in technology can yield significant returns in operational efficiency.