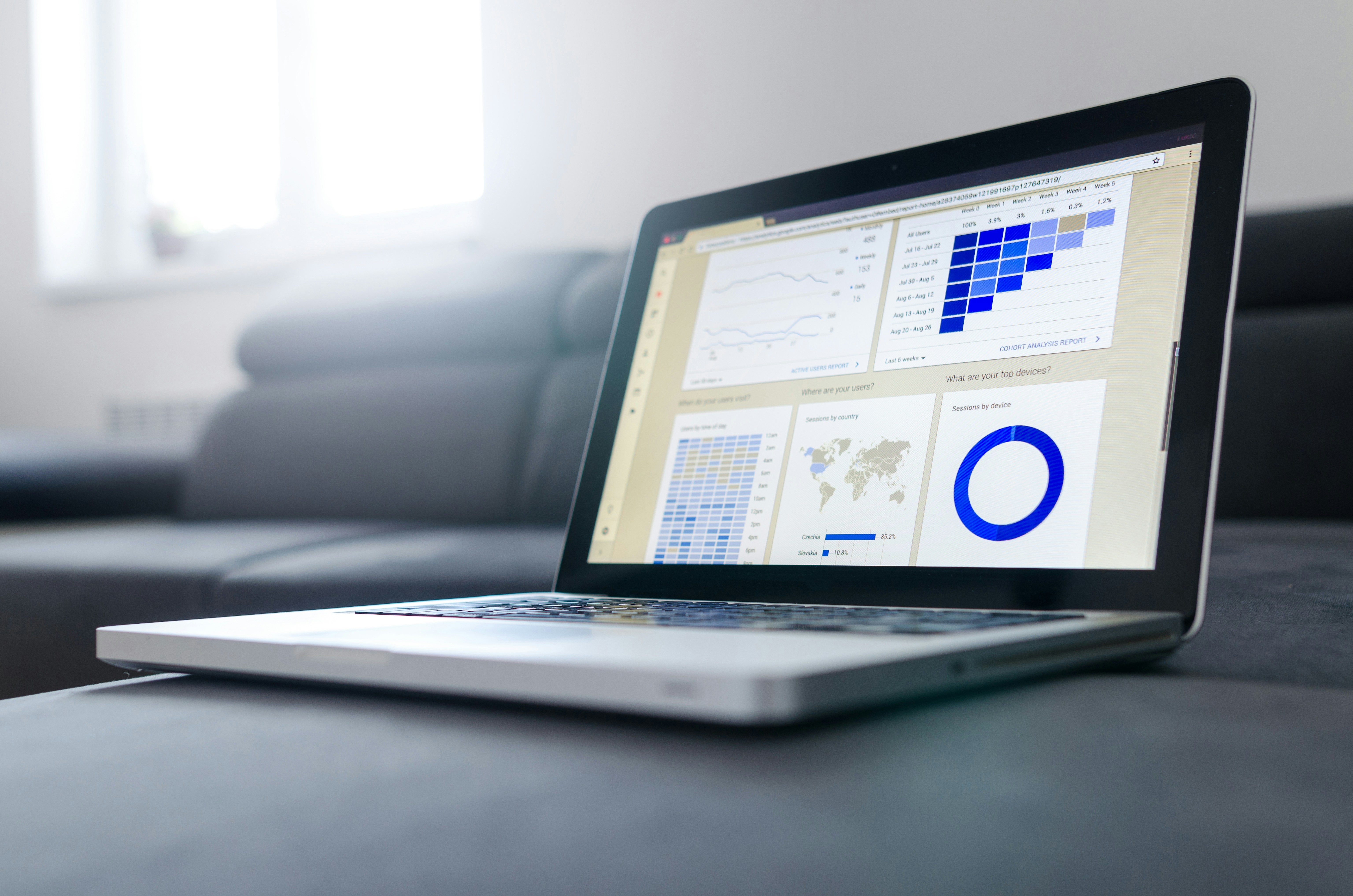
Introduction
Background of the Company
PacificLight Power Pte Ltd is a leading energy provider based in Singapore, specializing in power generation and retail electricity services. Serving over 30,000 commercial and industrial customers, the company plays a pivotal role in Singapore's energy sector. With a commitment to sustainability and operational excellence, PacificLight has established itself as a key player in meeting the nation's growing energy demands.
Purpose of the Case Study
This case study explores how PacificLight addressed significant challenges in its inventory management processes. The company struggled with inefficient inventory tracking, which led to delayed maintenance and inflated operational costs. We'll examine how the implementation of customized SAP MB52 reports resolved these challenges, aligning inventory processes with business goals to enhance efficiency and reduce lead times.
The Challenge
Detailed Description of the Problem
PacificLight's legacy inventory system relied on outdated, manual SAP MB52 reports that lacked real-time insights. This outdated system led to several critical issues:
- Stockouts and Overstocking: Inaccurate demand forecasting resulted in critical part shortages or excess inventory, impacting operational efficiency and tying up capital.
- Extended Lead Times: Delays in procuring materials slowed maintenance and repairs, potentially risking service reliability and customer satisfaction.
- High Operational Costs: Redundant stock and manual processes drained resources, affecting the company's bottom line and competitiveness in the market.
Why the Solution Was Urgent
With Singapore's energy demand on the rise, inefficient inventory management threatened PacificLight's ability to meet regulatory requirements and customer expectations. The company faced several risks if it failed to address these challenges:
- Potential penalties for non-compliance with regulatory standards
- Customer attrition due to service disruptions or delays
- Reputational damage in a highly competitive energy market
- Increased operational costs affecting profitability and market position
The Solution
Customized MB52 Reporting for Agile Inventory Management
To address these challenges, PacificLight implemented a solution that involved redesigning SAP's standard MB52 inventory reports to align with the company's specific workflows. The solution encompassed several key steps:
- Requirement Analysis: Collaborated with stakeholders across departments to identify gaps in data visibility and reporting needs.
- Customization: Developed dynamic dashboards featuring real-time stock levels, automated reorder alerts, and supplier lead time tracking.
- Integration: Ensured compatibility with existing ERP modules for seamless data flow and comprehensive inventory insights.
Key Features and Benefits
- Real-Time Insights: Provided instant access to inventory status across all warehouses, enabling proactive decision-making.
- Predictive Analytics: Implemented AI-driven demand forecasting to prevent stockouts and optimize inventory levels.
- User-Friendly Interface: Designed a simplified navigation system for faster decision-making and improved user adoption.
Implementation Process
Steps Taken
- Planning: Mapped existing processes and defined key performance indicators (KPIs) such as inventory turnover ratio and stockout frequency.
- Development: Employed iterative prototyping with continuous feedback from warehouse teams to ensure the solution met real-world needs.
- Training: Conducted comprehensive workshops to familiarize staff with the new system, ensuring smooth adoption and maximizing the benefits of the new tools.
- Deployment: Implemented a phased rollout across regional hubs to minimize disruption and allow for adjustments based on initial feedback.
Challenges Overcome
- Data Silos: Integrated disparate systems using API middleware, creating a unified view of inventory across the organization.
- User Resistance: Addressed through hands-on training sessions and by demonstrating the time-saving benefits of the new system, gradually building user confidence and adoption.
Results and Outcomes
Quantitative Results
- 70% Improvement in process efficiency through automated reporting, significantly reducing manual data entry and processing time.
- 15% Reduction in Lead Times, accelerating maintenance cycles and improving overall operational efficiency.
- 20% Cost Savings achieved from optimized stock levels, reducing both overstocking and emergency procurement needs.
Qualitative Outcomes
- Enhanced decision-making capabilities with real-time inventory insights
- Improved supplier relationships through more accurate and timely order placements
- Increased employee satisfaction due to streamlined processes and reduced manual workload
- Better compliance with regulatory requirements through improved tracking and reporting
Conclusion
Summary
PacificLight's inventory management overhaul showcases how tailored SAP solutions can effectively resolve operational bottlenecks in the energy sector. By replacing manual processes with intelligent, customized reporting, the company achieved significant improvements in agility, efficiency, and cost savings. This transformation not only addressed immediate inventory challenges but also positioned PacificLight for sustainable growth in a competitive market.
Lessons Learned
- Customization is Key: Off-the-shelf tools often fail to address the unique challenges of specific industries or organizations. Tailoring solutions to fit precise needs yields superior results.
- Stakeholder Collaboration: Involving end-users early and throughout the implementation process ensures higher adoption rates and more effective solutions that address real-world needs.
- Continuous Improvement: The success of this project highlighted the importance of regularly reviewing and updating systems to keep pace with evolving business needs and technological advancements.
- Data Integration: Breaking down data silos and creating a unified view of inventory data is crucial for making informed decisions and optimizing operations across the organization.